“Rod ends in bending”. How many times have we heard that phrase?
Teams are told regularly that it is a design feature that must be avoided and there is an unwritten rule at all Formula Student or Formula SAE events that a car with REIB in the suspension or steering system will not advance to the Design Finals.
At the Australian event a few years ago as the Tech Advisor I was determined that the Australian teams would not employ rod ends incorrectly and advised every team on their correct use. I thought it was a design demon that had been exorcised, yet at the very next competition, they were back!
Some teams argue passionately that if the rod ends are correctly sized, then the adjustability of threaded rod ends justifies their use. They point out that at one time most junior formula race cars used rod ends in this way as a matter of course. One of the most ardent FSAE judges against REIB was the late Carroll Smith, yet ironically, here is the cover picture from his Nuts, Bolts, Fasteners and Plumbing book showing him posed beside a REIB! To be fair, the heavily loaded lower wishbone has a proper encapsulated spherical bearing. The picture was taken by David Gooley.
Trying to justify REIB by saying they were used on some old FFord or F3 racecar is a flawed argument because these cars had neither the tyre grip nor the brake performance of modern cars, and so had lighter loads to react through the suspension links.
Certainly, every year cars with REIB finish the event, and some even finish high in the points, but this is not an excuse for poor design. So lets talk about why teams like REIB and why Design Judges hate them.
Teams like threaded rod ends because of the ease of adjustability. When a car uses suspension components incorporating them, the adjustment of camber and caster becomes a simple matter of twisting the rod end(s) in and out. Unfortunately, this usually means they are being loaded incorrectly. Threaded rod ends are designed to be loaded in compression or extension. That are not designed to be used when loaded laterally as this tends to bend the threaded shank and usually applies shear loads across the thread roots. Bending loads tend to distort the eye causing the spherical element to seize. This quickly leads to failure as shown below.
A rod end failure as shown here can be very dangerous as it can result in a sudden and complete loss of control. At the very least it will result in an instant DNF, ruining an entire year’s work for the team.
Judges can never condone a design feature that is inherently dangerous.
Of course if the rod ends are big enough they will not break, but the Design Judges argue that if the system is correctly designed, then smaller and lighter components can be used, and this has a flow on effect to the sizing of other components.
So the second objection that Judges have is related to Newtons Second Law. Cars that are heavier than necessary are not good designs.
The shear loads are not only in the vertical plane. Front wheel brake torque is the biggest single force in most cars, and this is reacted through the suspension links. If the car has outboard rear brakes, then there is a smaller brake torque force which must be reacted at the rear.
These forces are reacted in a horizontal plane, and if threaded rod ends are used, then a shear load is introduced. Failure of a rod end under hard braking can have catastrophic results, and as a result, the judges hate this aspect too.
Finally, the Judges do not like the offset load paths when rod ends are used in the wishbone construction. The cranked load path from the tyres into the chassis is not desirable. Sure, this aspect of design is not as critical as the potentially dangerous situations mentioned earlier, but it is still a factor in Design Judging.
Wishbones can be made with the rod ends mounted along the line of the legs. These are easy to make, but pose an installation problem if adjustments need to be made on the chassis end of the wishbone. This adjustment will change the length of the base, and will require the chassis mounts to have some form of adjustment or, heaven forbid, the wishbone legs to be bent or stressed. Needless to say, the design Judges don’t like this solution either.
The problem with wishbones using encapsulated spherical bearings is that they do not allow for easy adjustment. The usual method being the use of shims behind the chassis or upright mounted clevis, and here is another dilemma. The Design Judges hate thick stacks of shims so the range of adjustment is limited.
At the design stage, teams will not know the optimum suspension settings, and during the chassis build, construction errors may creep in, so suspension adjustability very desirable when testing and setting up the car.
My suggestion would be to make a set of adjustable wishbones using threaded rod ends. These can be used to set up the car prior to the event. Once the optimal geometry has been arrived at, then a set of fixed geometry wishbones using encapsulated spherical bearings, bushes or even flex plates, can be constructed for the event. The adjustable wishbones can be kept for use in an emergency.
I am looking forward to inspecting all the cars at Hockenheim in August and smiling because I see no “REIB”s. Well, even Design Judges can dream!
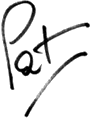
Pat