Another month means another column, welcome back to Pat's Corner.
I guess the most important that happened in the last month was the log jam that occurred when registration opened for FSG. The popularity of this event meant it was oversubscribed within minutes. This has happened recently at a few FSAE/FS type events. Usually, the response is “Sorry, you were too late, better luck next year”. Instead, the Steering Committee at FSG renegotiated with the insurers, the venue, the caterers, the judges etc, and then increased the entry by 20%. It's that sort of thinking that makes FSG the best event of its type in the world.
I have had some interesting correspondence about the spool drives discussed last month. Mostly, they were asking for clarification on some point or other. An interesting correspondent was Doug Milliken of RCVD fame who asked if I was proposing the existance of a 'virtual differential', arguing that a spool didn't permit the differing wheel speeds in cornering. The emails shuffled back and forth with Doug conceding that, although he didn't yet accept the idea of a 'virtual diff', he could see where a car could be set up to work with one. Anyone who watched the UQ car smoke the field in Autocross and Enduro at FSG '06 and inspected their tyres afterwards would be in no doubt that it can work, and work very well.
The Judges, Advisors and 'Experts' out there fall between two posts. At one end are what I call the 'Theoreticians' and at the other end we have what I call the 'Pragmatists'.
Judges like Doug and Claude Rouelle fall closer to the 'Theoretician' end, whilst those like Ron Tauranac fall at the other end of the scale. Ron is probably the most accomplished race car designer ever with numerous FI, GP, Indy etc wins credited to his designs as well as over 1600 very effective production race cars....all without the benefit of a University Degree in Math or Engineering. I would like to think that I fall somewhere between the two.
None of this makes the advice or input from these judges 'wrong', but like life, there are many ways to address the design task. Never forget that the most adaptable component in the car as well as a very powerful data analyser, is the driver. That's why you need good drivers.
This month I am going to talk about the importance of wheel balance.
Wheel Balance
Wheel balance is a major issue on both road cars and competition cars.
On a road car, an out of balance wheel will be felt by the occupants at about 100kph. Above and below this speed the vibration is not felt or is not objectionable.
The reason for this is that the frequency generated by the unbalanced wheel resonates with the spring frequency used by car makers to ensure good ride quality in the car.
A competition car will probably have a much higher spring frequency. This moves the resonance to a much higher wheel speed, and in concert with the stiff road springs, it may not be noticed.
Regardless of whether the imbalance is felt by the driver or not, the vibration caused excites the tyre rubber at the contact patch and will reduce mechanical grip. Remember, the wheel is vibrating at all speeds when it is unbalanced.
As an example, imagine your road car with a severely out of balance L/H front wheel. If you were to drive in R/H circles on a big skid pan at a speed where the steering is shaking, about 100kph, it is easy to understand why this unbalanced outer front wheel would destroy grip, causing the car to under-steer and run wide.
This effect exists at all speeds, even when the driver cannot feel the effect at the steering wheel, so satisfactory wheel balance is critical for good grip.
Balancing Modes
Static Balancing
As the word static implies, the tyre will be balanced when at rest. For example, if an unmoving assembly was centered on a cone and was balanced, it would be statically balanced. A “bubble balancer” is designed to statically balance a tyre/wheel assembly.
Static imbalance is where there is one amount of weight located in the centre of the wheel assembly causing an imbalance. As the weight rotates, centrifugal forces are created causing the wheel to lift as the weight reaches top dead center.
A statically imbalanced tyre driven for an extended period may cause ‘cupping’ in the tyre tread, create vibration, and adversely affect handling.
Static balancing alone is a seldom-recommended procedure that balances the assembly using only a single weight plane. For example, a single weight is commonly placed on the inner clip weight position for cosmetic purposes.
This is not a recommended practice and usually insures the assembly is not properly dynamically balanced. The assembly may then experience side-to-side imbalance while in motion, causing a shimmy condition and objectionable vibration.
Dynamic Balancing
Dynamic imbalance in general terms is defined where one or more locations of the tyre/wheel assembly are heavier causing an imbalance force and/or an imbalance wobble. This is particularly true with the wider tyre/wheel assemblies used in competition.
Shown below is a tyre/wheel assembly with two heavy spots of equal weight which are located 180° radially from each other on opposite sides. As this assembly rotates, centrifugal forces cause a large imbalance wobble to be created, but the imbalance force (as well as the static imbalance) will be zero.
Modern ‘dynamic’ balancers spin the wheel in order to measure both the up and down imbalance force and the wobble or shimmy related imbalance (side-to-side).
Dynamic balancers direct the operator to place correction weights on the inside and outside correction locations of the rim so that both imbalance force and imbalance wobble will be eliminated.
Note: There is no need to spin the tyre/wheel assembly at any particular speed to measure imbalance. Some perfectly acceptable hand spun dynamic balancers are available.
Finish Balancing
Also called ‘On-car balancing’. When the dynamically balanced wheel assembly is fitted to the vehicle, small amounts of imbalance may still exist.
These may be caused by slight radial clearances in the hub assembly; by manufacturing tolerance is the manufacture of the axle, hub and wheel assemblies, or slight imbalance in the brake rotor.
For best results, when the dynamically balanced wheel assembly is fitted to the vehicle, it should then be ‘finish balanced’.
On-car balancing should never be used as the primary method of wheel balancing.
Radial Force Variation
Ever had a tyre/wheel assembly that ‘wouldn’t balance’? By that I mean a wheel that ‘balanced’ on a balancing machine but still caused vibration when fitted to the car. The probable cause was radial force variation or radial run-out.
Radial force variation is an industrial measurement term describing the tyre uniformity under load, measuring the variation (up and down) of the load acting on the vehicle spindle.
All tyres have some non-uniformity in the sidewall and/or footprint due to variables in the manufacturing process. Tyre uniformity measurement values can be affected by rim width, rim condition and many diverse tyre mounting variables. Unlike balancing, there is often a small amount of RFV remaining in the wheel assembly and this is generally acceptable.
Radial Run-out
Run-out of the tyre/wheel assembly directly affects the amount of imbalance and should be corrected. The wheel assembly should be checked for both radial and lateral run-out. Run-out is checked first on the vehicle and then if necessary, off the vehicle.
Before checking for run-out, a careful inspection of the wheel assembly should be undertaken.
Ensure the tyre beads are correctly seated on the wheel and that there is no damage to either the wheel or the tyre. If the tyre tread is damaged from continual driving in an unbalanced condition, then that tyre should be replaced.
Ensure the wheel spins easily on the hub, and that the wheel bearings are correctly adjusted.
Once the run-out measurements have been made on the vehicle, if a significant amount of run-out has been detected, the wheel assembly should be checked for run-out off the vehicle. This is most easily done by mounting the wheel on a dynamic wheel balancing machine and spinning it by hand.
If there is a difference between the run-out measured on the car and run-out measured off the car, then the vehicle should be inspected for the following causes.
- Hub flange run-out
- Pitch circle run-out
- Rust, paint, debris or any other condition preventing the wheel from being mounted correctly.
Particular care should be taken if the vehicle has been fitted with after-market wheels. These wheels are often made for multiple applications, which may require differing spigot centering rings to be fitted. Remember, it is not the job of the studs to centre the wheels on the hub, so a team should machine their centering spigot to match the wheel.
Unloaded Radial Run-out
Checking for radial run-out should start with the wheel assembly fitted to the car. If the radial run-out is within specification, then no further checks need be made.
If the radial run-out exceeds specifications on the car, then the test should be repeated off the car. This will establish whether the problem is related to the wheel assembly, or a problem with the hub or wheel mounting on the vehicle. This off vehicle run-out check is most easily done on a wheel balancing machine.
If the off-vehicle check shows the wheel assembly is within specifications, then the problem is some form of eccentricity in the vehicle hub/axle or wheel mounting flange. Inspect carefully for corrosion or other debris preventing the wheel from being centered properly on the central spigot.
If the off-vehicle check shows excessive run-out, then it is necessary to isolate the problem to either the wheel or the tyre. If the wheel is an alloy casting which has been finish machined in the tyre mounting area, it will be necessary to demount the tyre so measurement for run-out can be made on the machined surface.
If the wheel does not run true, it must be repaired or replaced. If the wheel runs true, then the tyre must be replaced.
Unloaded Lateral Run-out
Checking for lateral run-out should start with the wheel assembly fitted to the car. If the radial run-out is within specification, then no further checks need be made.
If the lateral run-out exceeds specifications on the car, then the test should be repeated off the car. This will establish whether the problem is related to the wheel assembly, or a problem with the hub or wheel mounting on the vehicle.
This off vehicle run-out check is most easily done on a wheel balancing machine.
If the off vehicle check shows the run-out is within specification, then an issue exists with the hub/axle or wheel mounting flange. This can be checked for run-out by using a dial gauge and stand. Any excessive run-out must be repaired.
If the off vehicle check shows excessive run-out, then it is necessary to isolate the problem to either the wheel or the tyre. The usual cause is a buckled wheel, in which case the wheel must be repaired or replaced.
If the lateral run-out is in the tyre and not the wheel, then the tyre must be replaced.
Tyre Vibration Characteristics
Any tyre has natural frequency and vibration characteristics. When a tyre is subjected to a road contact at one point, it will vibrate at that point only at low speeds when the frequency of the applied force is below about 30 Hz.
When the frequency is higher, the entire tyre begins to vibrate.
A similar situation is caused when the tyre is ‘excited’ by the road surface irregularities.
These characteristics differ between radial and cross ply tyres due to the differing sidewall stiffness of each type.
Radial tyres have a lower natural frequency than cross ply tyres. This explains the different feel of each type of tyre under operating conditions.
Radials feel harsher as they transmit vibration at lower frequencies, whereas cross ply tyres transmit vibrations better at higher frequencies.
Finally, you are reminded that any vibration (whether you can feel it or not) will excite the tread rubber at the contact point and reduce mechanical grip.
Pats Design Error of the Month
This month I am going to revisit the problem of flexing wheel centres. You will recall a couple of issues ago I spoke about this and illustrated it with a picture of the TU Graz car exhibiting compliance on track. Some readers thought this was a veiled criticism of their carbon wheels. This is certainly not the case as I don't make veiled criticism of anything. If I have a criticism to make, I come right out and make it. On the record, the TU Graz carbon wheels were delightful!
In my archives I found this picture:
It shows severe compliance in the rear wheel, as the suspension design could never allow this amount of positive camber with the amount of chassis roll. The front wheel, which should be generating castor affected negative camber, is also allowing the tyre to roll over.
This will quickly ruin the tyres, but a closer inspection shows a more worrying problem, one I have also discussed before. Look at this picture:
This is the same wheel fitted to the teams previous car. The wheel is retained by 4 tapered wheel nuts tightened into an aluminium wheel centre. This raises stress around the bolt holes, and on a flexible wheel, will lead to total failure as happened on this similar wheel used by another Formula Student team:
Until next month, keep safe and don't fail to meat your deadlines.
Cheers
Pat
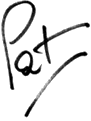